SMT utiliza solución y análisis de cavidades de soldadura por reflujo de aire en pasta de soldadura convencional (Edición Essence 2023), ¡te lo mereces!
1 Introducción

En el conjunto de la placa de circuito, primero se imprime pasta de soldadura en la almohadilla de soldadura de la placa de circuito y luego se fijan varios componentes electrónicos. Finalmente, después del horno de reflujo, se funden las perlas de estaño en la pasta de soldadura y se sueldan todo tipo de componentes electrónicos y la almohadilla de soldadura de la placa de circuito para realizar el ensamblaje de submódulos eléctricos. La tecnología de montaje en superficie (sMT) se utiliza cada vez más en productos de embalaje de alta densidad, como paquetes a nivel de sistema (siP), dispositivos Ballgridarray (BGA) y paquetes de chip plano y cuadrado sin clavijas (quad aatSin plomo, denominado QFN). ) dispositivo.
Debido a las características del proceso y los materiales de soldadura en pasta, después de la soldadura por reflujo de estos dispositivos de gran superficie de soldadura, habrá agujeros en el área de soldadura, lo que afectará las propiedades eléctricas, térmicas y mecánicas del producto. Incluso conducir a fallas del producto, por lo tanto, mejorar la cavidad de soldadura por reflujo de pasta de soldadura se ha convertido en un proceso y un problema técnico que debe resolverse, algunos investigadores han analizado y estudiado las causas de la cavidad de soldadura de bolas de soldadura BGA y han proporcionado soluciones de mejora, soldadura convencional. proceso de soldadura por reflujo de pasta área de soldadura de Falta una solución de chip desnudo de QFN superior a 10 mm2 o área de soldadura superior a 6 mm2.
Utilice soldadura Preformsolder y soldadura en horno de reflujo al vacío para mejorar el orificio de soldadura. La soldadura prefabricada requiere equipo especial para apuntar el fundente. Por ejemplo, el chip se desplaza e inclina seriamente después de colocarlo directamente sobre la soldadura prefabricada. Si el chip de montaje fundente se refluye y luego se apunta, el proceso aumenta en dos reflujos y el costo de la soldadura prefabricada y el material fundente es mucho mayor que el de la soldadura en pasta.
El equipo de reflujo al vacío es más caro, la capacidad de vacío de la cámara de vacío independiente es muy baja, el rendimiento de costos no es alto y el problema de las salpicaduras de estaño es grave, lo cual es un factor importante en la aplicación de alta densidad y paso pequeño. productos. En este artículo, basado en el proceso de soldadura por reflujo en pasta convencional, se desarrolla e introduce un nuevo proceso de soldadura por reflujo secundario para mejorar la cavidad de soldadura y resolver los problemas de unión y agrietamiento del sello plástico causados por la cavidad de soldadura.
2 Mecanismo de producción y cavidad de soldadura por reflujo de impresión de pasta de soldadura
2.1 Cavidad de soldadura
Después de la soldadura por reflujo, el producto se probó bajo rayos X. Se descubrió que los orificios en la zona de soldadura con un color más claro se debían a una soldadura insuficiente en la capa de soldadura, como se muestra en la Figura 1.
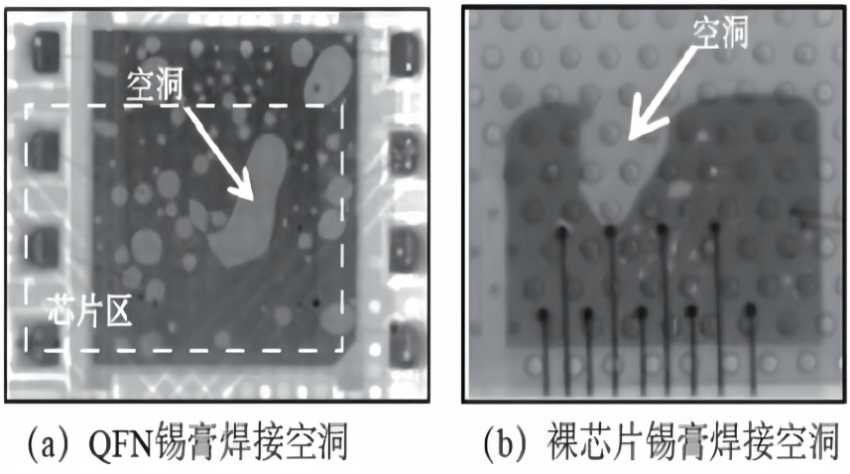
Detección por rayos X del agujero de la burbuja.
2.2 Mecanismo de formación de la cavidad de soldadura.
Tomando como ejemplo la soldadura en pasta sAC305, la composición y función principales se muestran en la Tabla 1. Las perlas de fundente y estaño están unidas entre sí en forma de pasta. La relación en peso entre soldadura de estaño y fundente es de aproximadamente 9:1 y la relación en volumen es de aproximadamente 1:1.
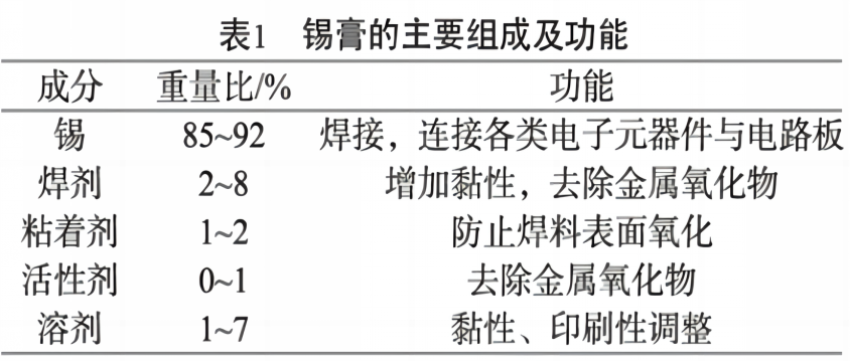
Después de imprimir y montar la soldadura en pasta con varios componentes electrónicos, la soldadura en pasta pasará por cuatro etapas de precalentamiento, activación, reflujo y enfriamiento cuando pasa por el horno de reflujo. El estado de la soldadura en pasta también es diferente con diferentes temperaturas en diferentes etapas, como se muestra en la Figura 2.
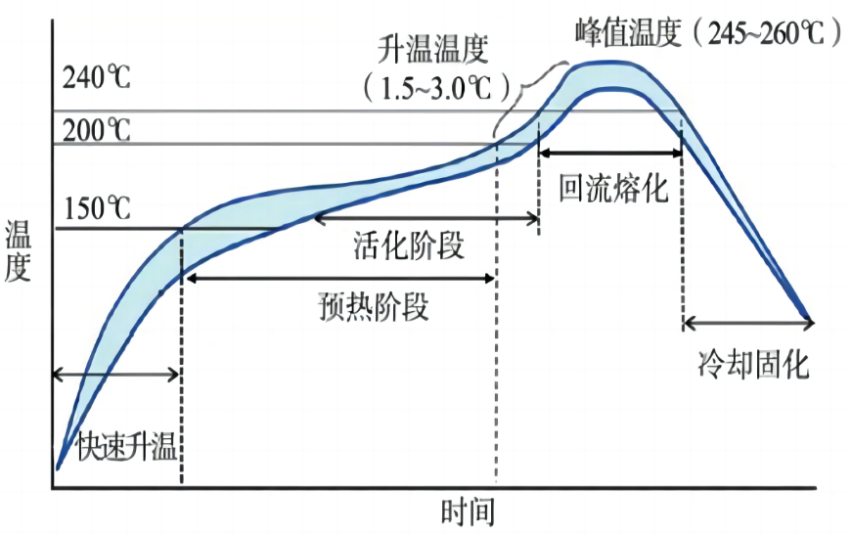
Referencia de perfil para cada área de soldadura por reflujo
En las etapas de precalentamiento y activación, los componentes volátiles del fundente de la soldadura en pasta se volatilizarán hasta convertirse en gas cuando se calienten. Al mismo tiempo, se producirán gases cuando se elimine el óxido de la superficie de la capa de soldadura. Algunos de estos gases se volatilizarán y abandonarán la pasta de soldadura, y las perlas de soldadura se condensarán fuertemente debido a la volatilización del fundente. En la etapa de reflujo, el fundente restante en la soldadura en pasta se evaporará rápidamente, las perlas de estaño se derretirán, una pequeña cantidad de gas volátil del fundente y la mayor parte del aire entre las perlas de estaño no se dispersarán a tiempo, y el residuo en el El estaño fundido y bajo la tensión del estaño fundido tienen una estructura tipo sándwich de hamburguesa y quedan atrapados por la almohadilla de soldadura de la placa de circuito y los componentes electrónicos, y el gas envuelto en el estaño líquido es difícil de escapar solo por la flotabilidad hacia arriba. El tiempo de fusión superior. es muy corto. Cuando el estaño fundido se enfría y se convierte en estaño sólido, aparecen poros en la capa de soldadura y se forman orificios de soldadura, como se muestra en la Figura 3.
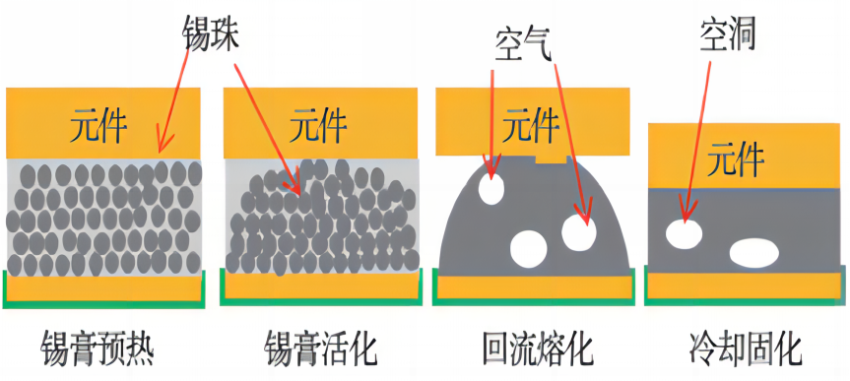
Diagrama esquemático del vacío generado por la soldadura por reflujo en pasta de soldadura
La causa principal de la cavidad de soldadura es que el aire o el gas volátil envuelto en la pasta de soldadura después de la fusión no se descarga por completo. Los factores que influyen incluyen el material de la pasta de soldadura, la forma de impresión de la pasta de soldadura, la cantidad de impresión de la pasta de soldadura, la temperatura de reflujo, el tiempo de reflujo, el tamaño de la soldadura, la estructura, etc.
3. Verificación de los factores que influyen en los orificios de soldadura por reflujo de impresión de pasta de soldadura
Se utilizaron pruebas QFN y de chip desnudo para confirmar las causas principales de los huecos de la soldadura por reflujo y para encontrar formas de mejorar los huecos de la soldadura por reflujo impresos con pasta de soldadura. El perfil del producto de soldadura por reflujo de pasta de soldadura QFN y de chip desnudo se muestra en la Figura 4. El tamaño de la superficie de soldadura QFN es de 4,4 mm x 4,1 mm, la superficie de soldadura es una capa estañada (100% estaño puro); El tamaño de soldadura del chip desnudo es de 3,0 mm x 2,3 mm, la capa de soldadura es una capa bimetálica de níquel-vanadio pulverizada y la capa superficial es vanadio. La almohadilla de soldadura del sustrato era de inmersión en oro de níquel-paladio no electrolítico y el espesor era de 0,4 μm/0,06 μm/0,04 μm. Se utiliza soldadura en pasta SAC305, el equipo de impresión de soldadura en pasta es DEK Horizon APix, el equipo del horno de reflujo es BTUPyramax150N y el equipo de rayos X es DAGExD7500VR.
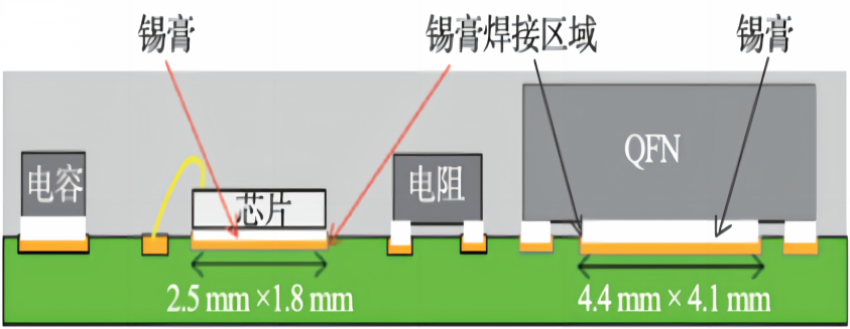
Planos de soldadura QFN y de chip desnudo
Para facilitar la comparación de los resultados de las pruebas, la soldadura por reflujo se realizó en las condiciones de la Tabla 2.
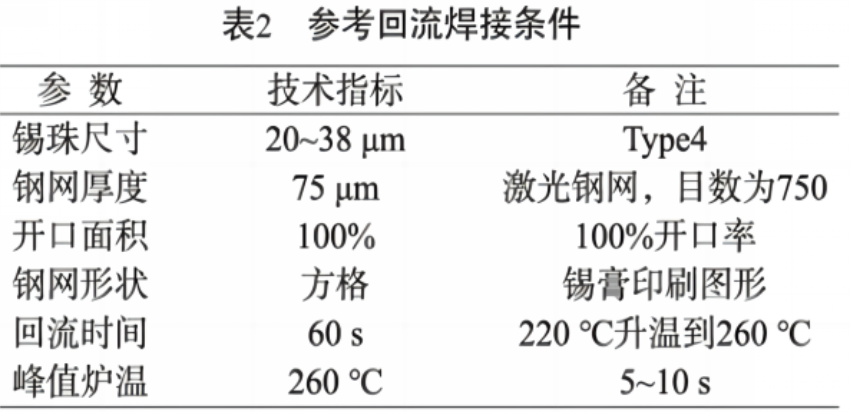
Tabla de condiciones de soldadura por reflujo
Después de completar el montaje de la superficie y la soldadura por reflujo, la capa de soldadura se detectó mediante rayos X y se encontró que había grandes agujeros en la capa de soldadura en la parte inferior del QFN y virutas desnudas, como se muestra en la Figura 5.
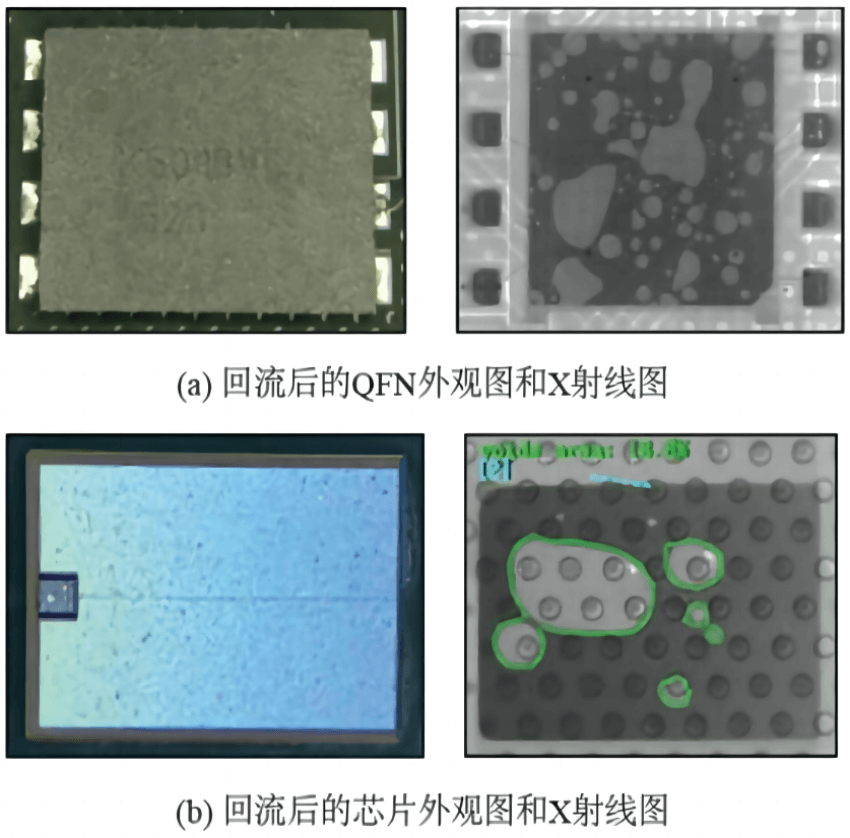
QFN y holograma de chip (rayos X)
Dado que el tamaño del cordón de estaño, el espesor de la malla de acero, la tasa del área de apertura, la forma de la malla de acero, el tiempo de reflujo y la temperatura máxima del horno afectarán los huecos de la soldadura por reflujo, existen muchos factores que influyen, que se verificarán directamente mediante la prueba DOE y el número de pruebas experimentales. Los grupos serán demasiado grandes. Es necesario detectar y determinar rápidamente los principales factores de influencia mediante una prueba de comparación de correlación y luego optimizar aún más los principales factores de influencia a través del DOE.
3.1 Dimensiones de los orificios de soldadura y las perlas de estaño en pasta de soldadura
Con la prueba de soldadura en pasta SAC305 tipo 3 (tamaño del cordón 25-45 μm), otras condiciones permanecen sin cambios. Después del reflujo, se miden los orificios en la capa de soldadura y se comparan con la soldadura en pasta tipo 4. Se encuentra que los orificios en la capa de soldadura no son significativamente diferentes entre los dos tipos de soldadura en pasta, lo que indica que la soldadura en pasta con diferente tamaño de cordón no tiene una influencia obvia en los orificios en la capa de soldadura, lo cual no es un factor de influencia. como se muestra en la FIG. 6 Como se muestra.
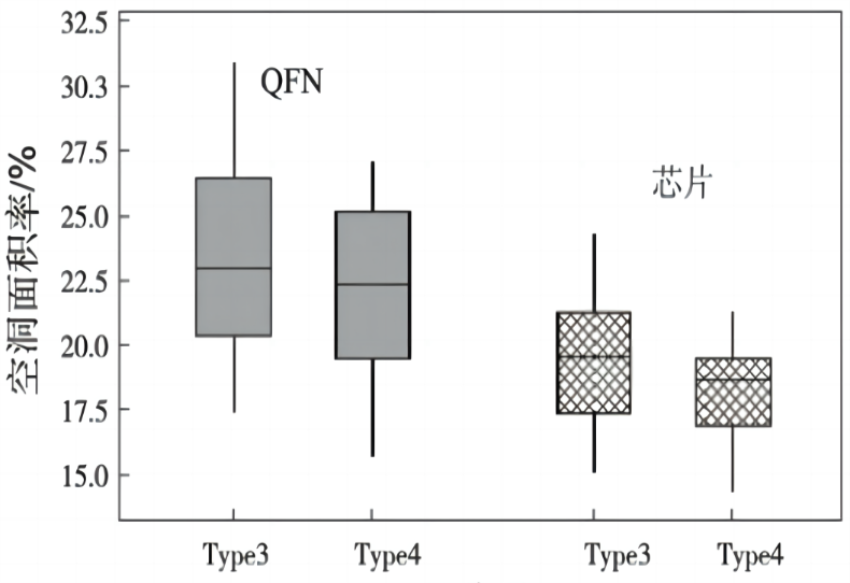
Comparación de agujeros de polvo de estaño metálico con diferentes tamaños de partículas.
3.2 Espesor de la cavidad de soldadura y malla de acero impresa.
Después del reflujo, el área de la cavidad de la capa soldada se midió con la malla de acero impresa con un espesor de 50 µm, 100 µm y 125 µm, y otras condiciones permanecieron sin cambios. Se encontró que el efecto de diferentes espesores de malla de acero (pasta de soldadura) en QFN se comparó con el de la malla de acero impresa con un espesor de 75 μm. A medida que aumenta el espesor de la malla de acero, el área de la cavidad disminuye gradualmente. Después de alcanzar un cierto espesor (100 μm), el área de la cavidad se invertirá y comenzará a aumentar con el aumento del espesor de la malla de acero, como se muestra en la Figura 7.
Esto muestra que cuando se aumenta la cantidad de pasta de soldadura, el estaño líquido con reflujo queda cubierto por el chip y la salida de aire residual es sólo estrecha en cuatro lados. Cuando se cambia la cantidad de pasta de soldadura, la salida de escape de aire residual también aumenta, y la ráfaga instantánea de aire envuelto en estaño líquido o gas volátil que escapa del estaño líquido hará que el estaño líquido salpique alrededor del QFN y el chip.
La prueba encontró que con el aumento del espesor de la malla de acero, el estallido de burbujas causado por el escape de aire o gas volátil también aumentará, y la probabilidad de que el estaño salpique alrededor del QFN y el chip también aumentará en consecuencia.
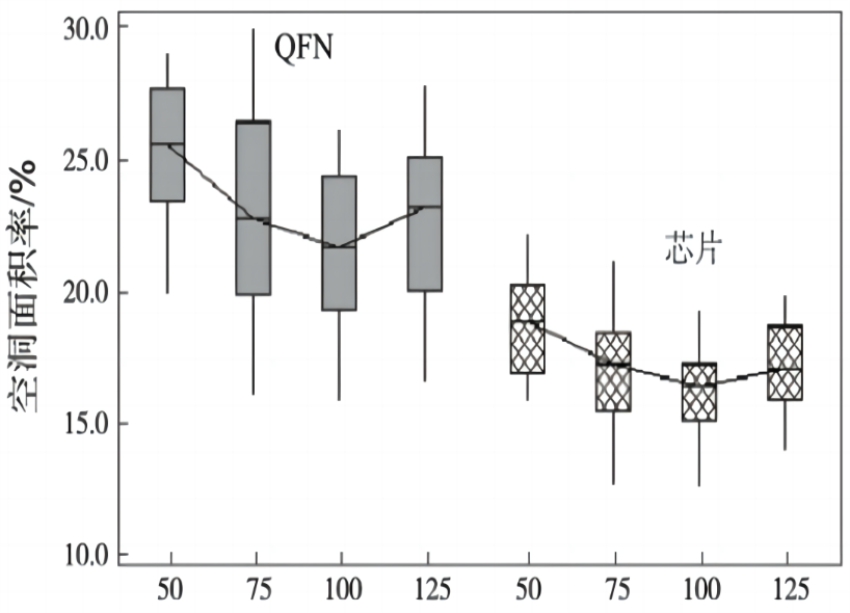
Comparación de agujeros en mallas de acero de diferente espesor.
3.3 Relación de área de la cavidad de soldadura y la abertura de la malla de acero
Se probó la malla de acero impresa con una tasa de apertura del 100%, 90% y 80%, y las demás condiciones permanecieron sin cambios. Después del reflujo, se midió el área de la cavidad de la capa soldada y se comparó con la malla de acero impresa con una tasa de apertura del 100 %. Se encontró que no había diferencias significativas en la cavidad de la capa soldada bajo las condiciones de tasa de apertura de 100% y 90% 80%, como se muestra en la Figura 8.
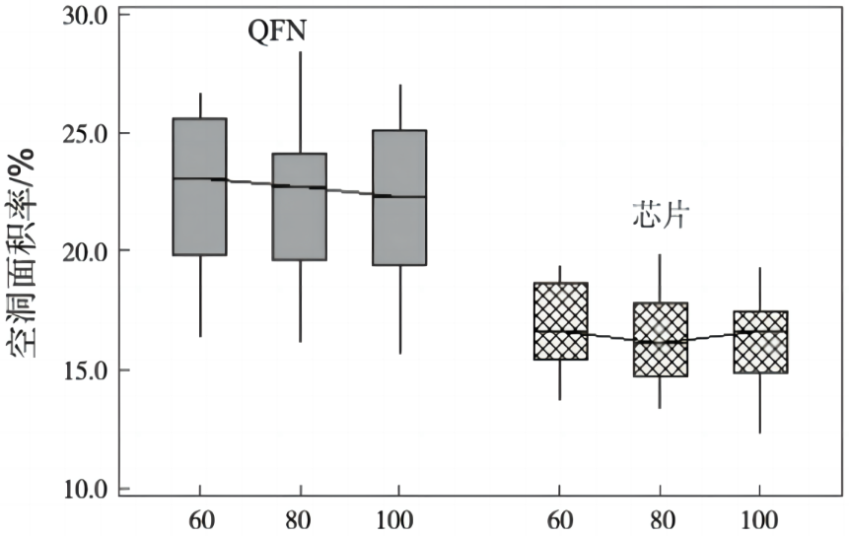
Comparación de cavidades de diferentes áreas de apertura de diferentes mallas de acero
3.4 Cavidad soldada y forma de malla de acero impresa.
Con la prueba de forma de impresión de la pasta de soldadura de la tira by la rejilla inclinada c, otras condiciones permanecen sin cambios. Después del reflujo, se mide el área de la cavidad de la capa de soldadura y se compara con la forma de impresión de la rejilla a. Se encuentra que no hay diferencia significativa en la cavidad de la capa de soldadura bajo las condiciones de rejilla, tira y rejilla inclinada, como se muestra en la Figura 9.
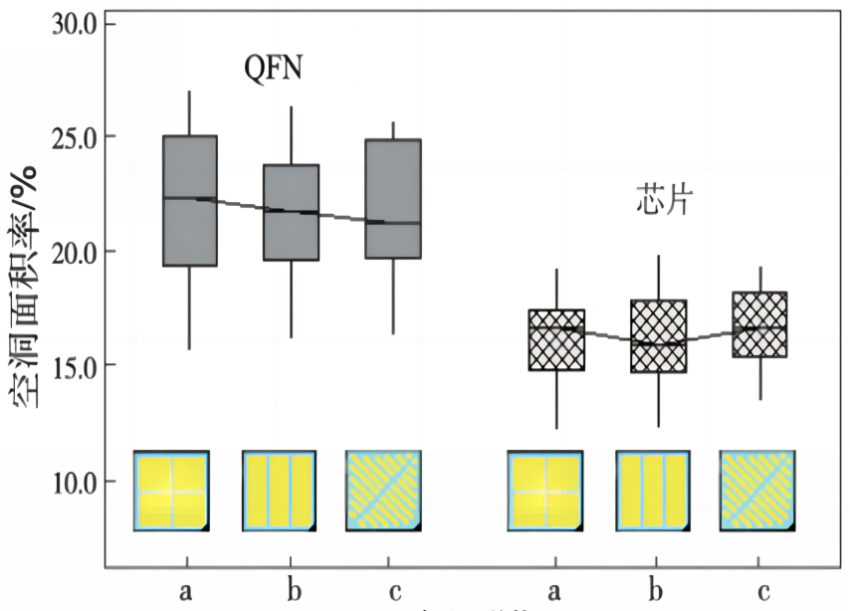
Comparación de agujeros en diferentes modos de apertura de malla de acero.
3.5 Cavidad de soldadura y tiempo de reflujo.
Después de una prueba de tiempo de reflujo prolongado (70 s, 80 s, 90 s), otras condiciones permanecen sin cambios, se midió el agujero en la capa de soldadura después del reflujo y se comparó con el tiempo de reflujo de 60 s, se encontró que con el aumento de tiempo de reflujo, el área del orificio de soldadura disminuyó, pero la amplitud de reducción disminuyó gradualmente con el aumento del tiempo, como se muestra en la Figura 10. Esto muestra que en el caso de un tiempo de reflujo insuficiente, aumentar el tiempo de reflujo es Propicio para el desbordamiento total del aire envuelto en estaño líquido fundido, pero después de que el tiempo de reflujo aumenta hasta cierto tiempo, es difícil que el aire envuelto en estaño líquido vuelva a desbordarse. El tiempo de reflujo es uno de los factores que afectan la cavidad de soldadura.
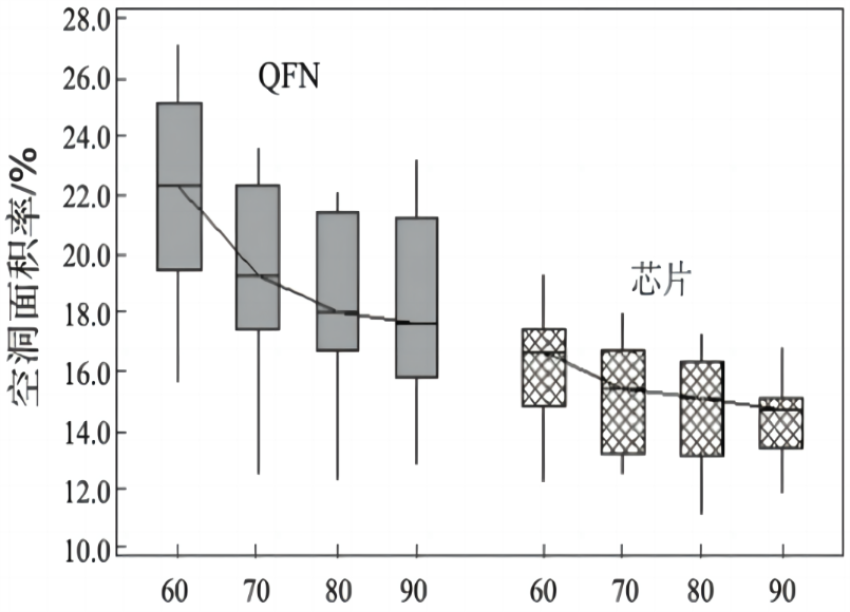
Comparación nula de diferentes duraciones de reflujo
3.6 Cavidad de soldadura y temperatura máxima del horno.
Con la prueba de temperatura máxima del horno de 240 ℃ y 250 ℃ y otras condiciones sin cambios, se midió el área de la cavidad de la capa soldada después del reflujo, y en comparación con la temperatura máxima del horno de 260 ℃, se encontró que bajo diferentes condiciones de temperatura máxima del horno, la cavidad de la capa soldada de QFN y el chip no cambió significativamente, como se muestra en la Figura 11. Muestra que diferentes temperaturas máximas del horno no tienen ningún efecto obvio en QFN y el orificio en la capa de soldadura. del chip, que no influye.
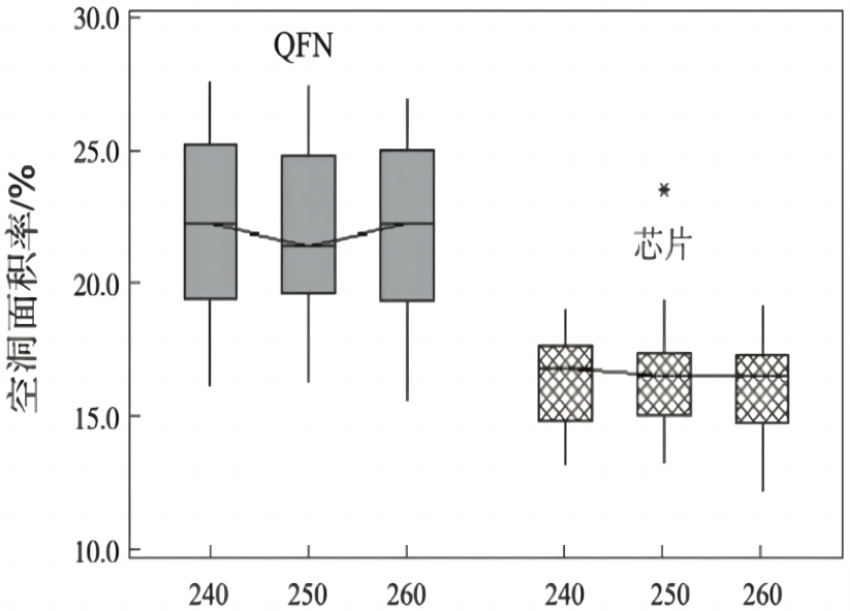
Comparación nula de diferentes temperaturas máximas
Las pruebas anteriores indican que los factores importantes que afectan la cavidad de la capa de soldadura de QFN y la viruta son el tiempo de reflujo y el espesor de la malla de acero.
4 Mejora de la cavidad de soldadura por reflujo con impresión de pasta de soldadura
Prueba 4.1DOE para mejorar la cavidad de soldadura.
Se mejoró el agujero en la capa de soldadura de QFN y viruta encontrando el valor óptimo de los principales factores que influyen (tiempo de reflujo y espesor de la malla de acero). La pasta de soldadura era SAC305 tipo 4, la forma de la malla de acero era tipo rejilla (grado de apertura del 100%), la temperatura máxima del horno fue de 260 ℃ y otras condiciones de prueba fueron las mismas que las del equipo de prueba. La prueba DOE y los resultados se muestran en la Tabla 3. Las influencias del espesor de la malla de acero y el tiempo de reflujo en QFN y los orificios de soldadura de viruta se muestran en la Figura 12. A través del análisis de interacción de los principales factores que influyen, se encuentra que usando un espesor de malla de acero de 100 μm y el tiempo de reflujo de 80 s puede reducir significativamente la cavidad de soldadura de QFN y chip. La tasa de cavidad de soldadura de QFN se reduce del máximo 27,8% al 16,1%, y la tasa de cavidad de soldadura de viruta se reduce del máximo 20,5% al 14,5%.
En la prueba, se produjeron 1000 productos en las condiciones óptimas (espesor de malla de acero de 100 μm, tiempo de reflujo de 80 s) y se midió aleatoriamente la velocidad de la cavidad de soldadura de 100 QFN y la viruta. La tasa de cavidad de soldadura promedio de QFN fue del 16,4% y la tasa de cavidad de soldadura promedio del chip fue del 14,7%. La tasa de cavidad de soldadura del chip y el chip se reducen obviamente.
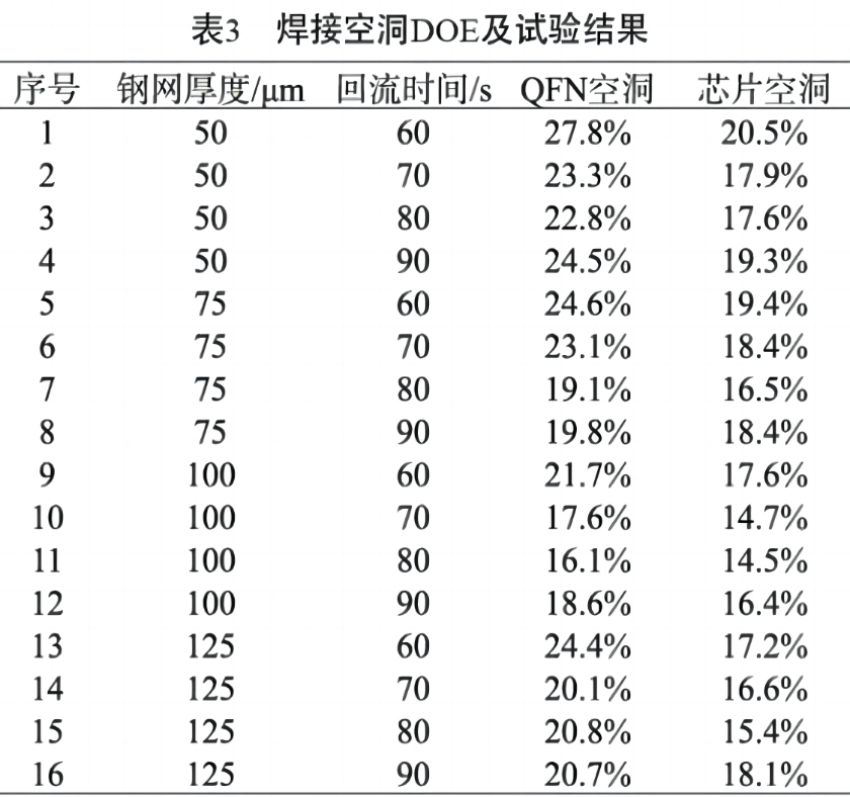
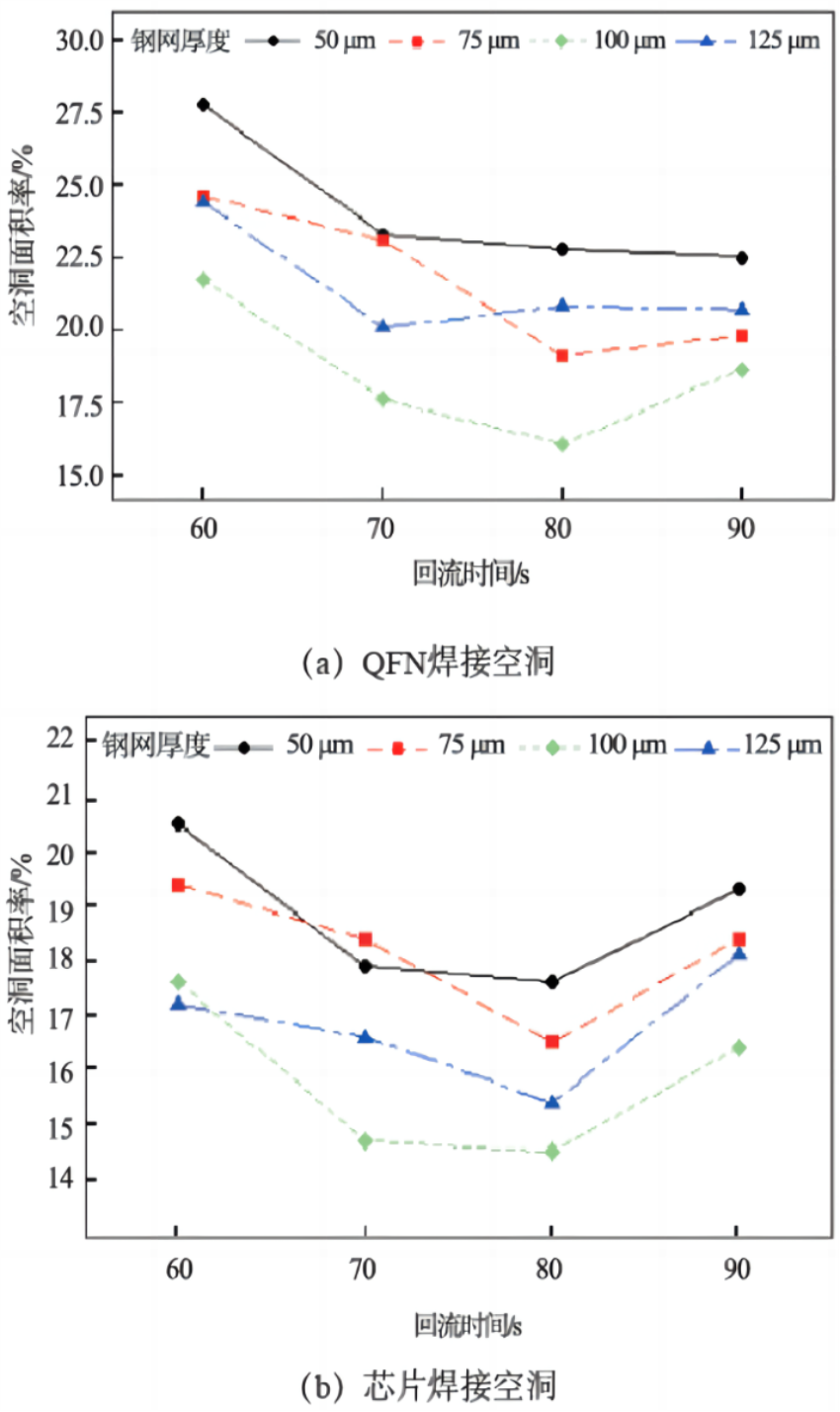
4.2 El nuevo proceso mejora la cavidad de soldadura
La situación de producción real y las pruebas muestran que cuando el área de la cavidad de soldadura en la parte inferior del chip es inferior al 10%, el problema de agrietamiento en la posición de la cavidad del chip no ocurrirá durante la unión y el moldeado del plomo. Los parámetros del proceso optimizados por el DOE no pueden cumplir con los requisitos de análisis y resolución de orificios en la soldadura por reflujo de pasta de soldadura convencional, y es necesario reducir aún más la tasa del área de la cavidad de soldadura del chip.
Dado que el chip cubierto por la soldadura evita que se escape el gas de la soldadura, la tasa de orificios en la parte inferior del chip se reduce aún más eliminando o reduciendo el gas recubierto de soldadura. Se adopta un nuevo proceso de soldadura por reflujo con dos impresiones de soldadura en pasta: una impresión en pasta de soldadura, una impresión por reflujo que no cubre QFN y un chip desnudo que descarga el gas en la soldadura; El proceso específico de impresión secundaria de soldadura en pasta, parche y reflujo secundario se muestra en la Figura 13.
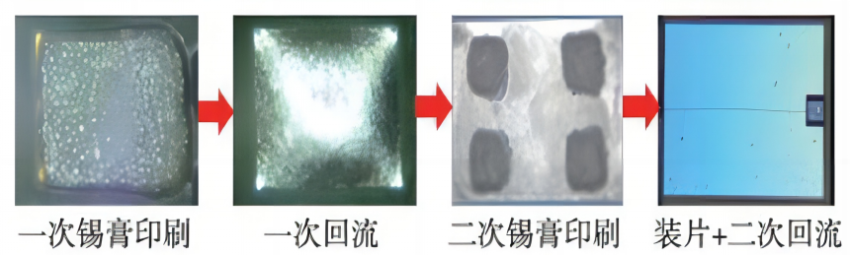
Cuando se imprime por primera vez la pasta de soldadura de 75 μm de espesor, la mayor parte del gas en la soldadura sin cubierta de chip se escapa de la superficie y el espesor después del reflujo es de aproximadamente 50 μm. Después de completar el reflujo primario, se imprimen pequeños cuadrados en la superficie de la soldadura solidificada enfriada (para reducir la cantidad de soldadura en pasta, reducir la cantidad de derrame de gas, reducir o eliminar salpicaduras de soldadura) y la soldadura en pasta con un espesor de 50 μm (los resultados de las pruebas anteriores muestran que 100 μm es lo mejor, por lo que el espesor de la impresión secundaria es 100 μm. 50 μm = 50 μm), luego instale el chip y luego regrese hasta los 80 s. Casi no hay orificios en la soldadura después de la primera impresión y reflujo, y la pasta de soldadura en la segunda impresión es pequeña y el orificio de soldadura es pequeño, como se muestra en la Figura 14.
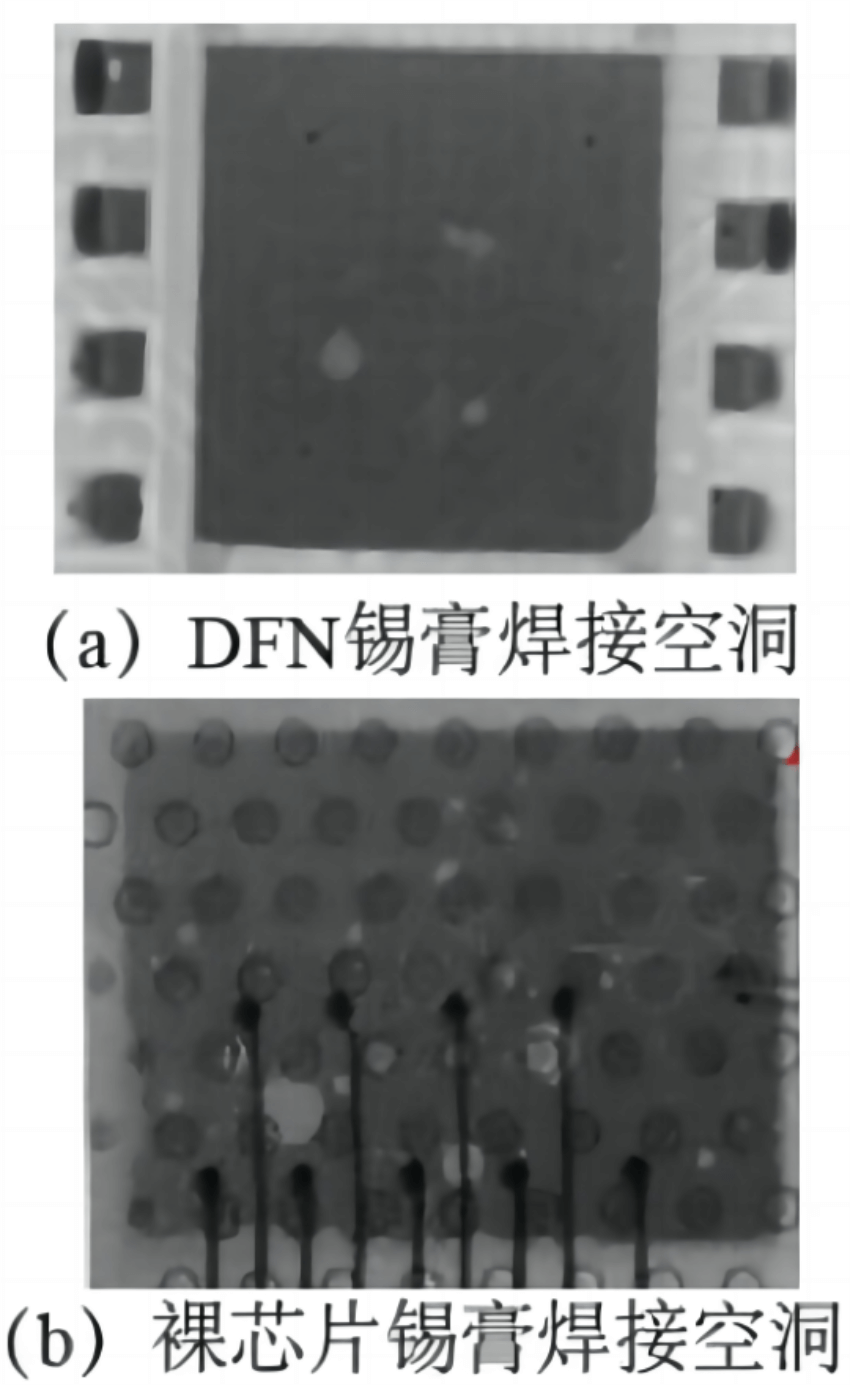
Después de dos impresiones de soldadura en pasta, dibujo hueco.
4.3 Verificación del efecto de cavidad de soldadura
La producción de 2000 productos (el espesor de la primera malla de acero de impresión es de 75 μm, el espesor de la segunda malla de acero de impresión es de 50 μm), otras condiciones sin cambios, la medición aleatoria de 500 QFN y la tasa de cavidad de soldadura de viruta, encontraron que el nuevo proceso después del primer reflujo no hay cavidad, después del segundo reflujo QFN La tasa máxima de cavidad de soldadura es del 4,8% y la tasa máxima de cavidad de soldadura del chip es del 4,1%. En comparación con el proceso de soldadura de impresión de pasta única original y el proceso optimizado DOE, la cavidad de soldadura se reduce significativamente, como se muestra en la Figura 15. No se encontraron grietas por viruta después de las pruebas funcionales de todos los productos.
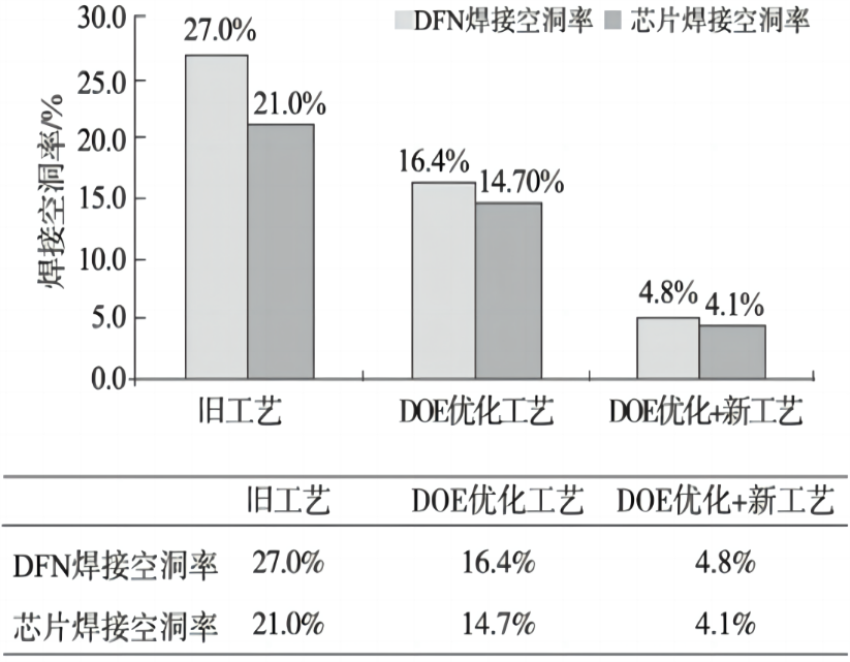
5 Resumen
La optimización de la cantidad de impresión de pasta de soldadura y el tiempo de reflujo puede reducir el área de la cavidad de soldadura, pero la tasa de cavidad de soldadura sigue siendo grande. El uso de dos técnicas de soldadura por reflujo con impresión de pasta de soldadura puede maximizar de manera efectiva y máxima la tasa de cavidad de soldadura. El área de soldadura del chip desnudo del circuito QFN puede ser de 4,4 mm x 4,1 mm y 3,0 mm x 2,3 mm respectivamente en la producción en masa. La tasa de cavidad de la soldadura por reflujo se controla por debajo del 5%, lo que mejora la calidad y confiabilidad de la soldadura por reflujo. La investigación contenida en este artículo proporciona una referencia importante para mejorar el problema de la cavidad de soldadura en superficies de soldadura de gran superficie.